在工厂的生产全流程相关业务中,工艺工作处于基础与先导地位。如果说设备是工厂的肌肉,传感器和网络是工厂的神经,那么工艺则是工厂的灵魂。因此,改进工艺工作势在必行。
第一,工艺工作的改进要从精益优化现有工艺开始,实行工艺标准化,推广工艺精益化,研究工艺稳健化。无论是传统生产方式还是工业4.0环境下的智能工厂,都需要有精益稳定的制造工艺,这也是解决我们目前效率和质量问题的根本途径。所谓智能工厂的“智能”是技术人员将一系列的判断因素、思考逻辑,根据具体的业务流程进行提炼而形成的,与人类的智能不可相提并论。因此,其对制造工艺的要求比传统的生产方式要高很多,不完善的工艺在目前的状况下只会导致我们的生产效率低下、产品质量不稳定,但在工业4.0环境下,不稳定的工艺规程则会出现预测外错误,使智能工厂终止运行,造成重大损失。第二,为使工艺精益稳健,我们不能再使用依靠实际生产进行的验证方式,而要引入工业4.0的一个重要概念-数字双胞胎,就是将现实中的环境与状态,在虚拟的数字空间中模拟出来,创造一个与真实工厂一模一样的虚拟数字工厂,虚拟现实环境,对工艺、流程、规划等进行验证、反馈和完善。无论是加工过程中的细节还是宏观工艺布局规划的运行情况,都可以在虚拟的数字工厂中进行验证测试,这将极大地提高工作的成熟度,节省大量的时间与资源。
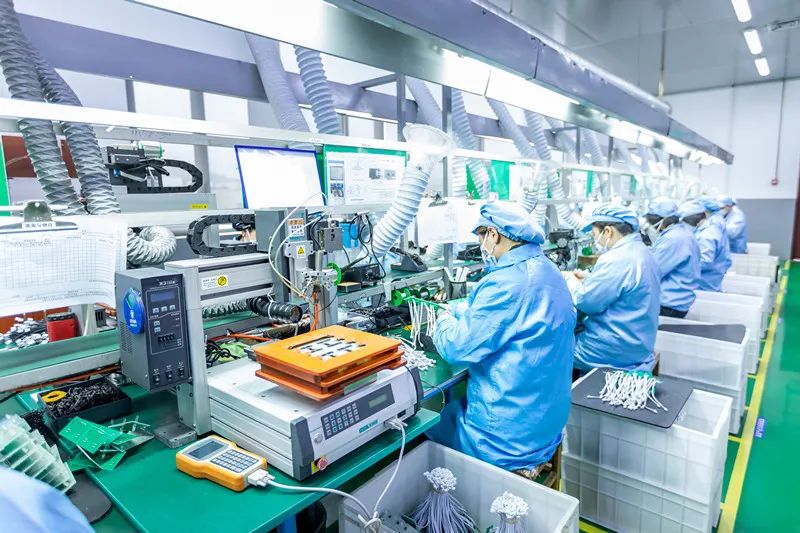
我们在工艺中如铸造、焊接、钣金、机械加工等专业,已经开始采用模拟仿真,但目前使用范围较小,规范性也不够,此后应制定详细计划,建立好模拟仿真环境,拓展模拟仿真领域,使模拟仿真真正起到效果,逐步实现全环境的实时模拟。第三,要转变工艺思想。一切变革最开始都是源于思想的转变,传统工艺员的主要工作是编制单一流程的工艺规程,在未来,工艺技术人员的主要工作将是提炼工艺思考逻辑,不断地补充、完善、优化庞大的工艺数据库,维护工艺知识数据,而实际的工艺设计工作将可能由计算机来完成。工艺规程也将不再是单一流程的形式,而是多流程离散型的工艺流程,在保证产品质量的情况下,使工艺路线尽可能地灵活,以便为智能工厂的决策系统提供尽可能多的选择,通过统筹分析各影响因素,安排最优的路线。
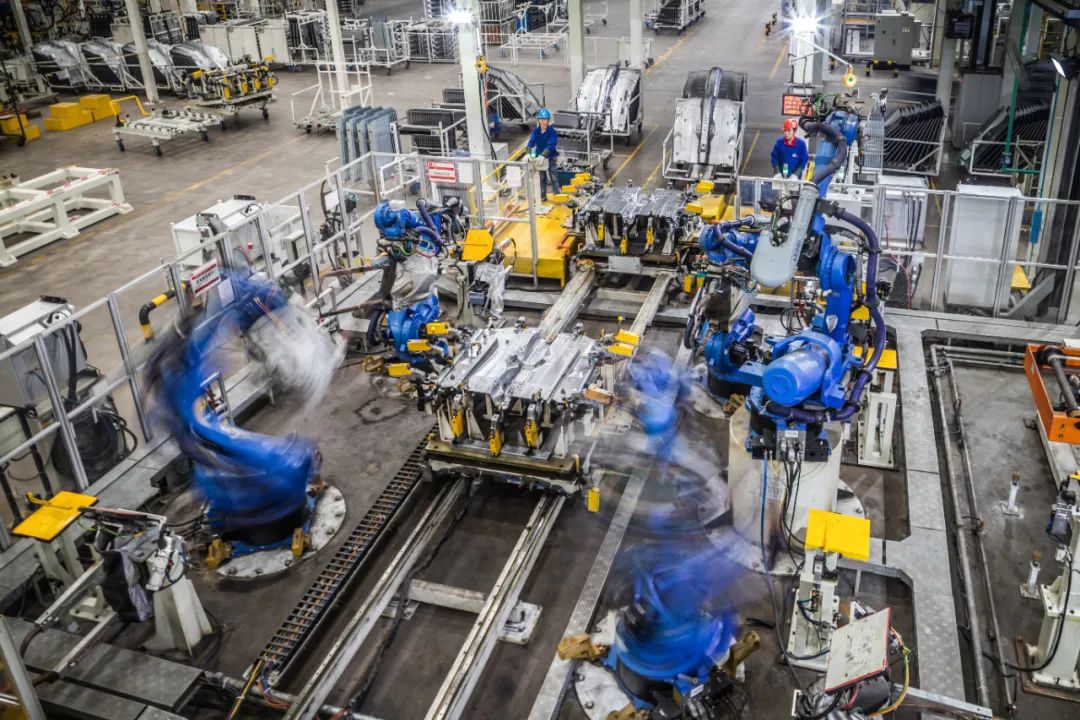
不合时宜的传统工艺思想也要摒除,最典型的是装夹找正和入体公差的标注习惯。在目前的生产过程中,机床上的装夹找正浪费了大量的机床工作时间,严重影响了生产效率。由于机械加工精度的不断提高和机床功能的增多,装夹找正问题已经可以通过精密定位夹具和机床的自找正功能实现。入体公差的标注习惯则是因为过去以普通机床加工为主,为了降低人为加工超差概率,提高产品合格率而采取的手段,这使得产品的实际加工尺寸偏离了正态分布,不利于保证批量产品的质量稳定性。目前数控加工设备已大范围应用,加工精度较以前也大为提高,不必再要求工艺尺寸采用入体公差标注。第四,研究机器人和快换夹具的应用。工业4.0要实现的智能化并不是要取代人,智能工厂并不是无人工厂,而是为了使人和机器更好地配合,实现更高的劳动生产率。为此,在智能工厂中,要努力消除人的不稳定因素。根据制造业目前的状况想要实现高度的无人自动化生产,既不现实,也不经济,在适合的环节引入机器人,是提高稳定性和效率最好的选择。机器人与快换夹具的配合使用,可以适应多品种少批量的生产,在保证柔性的情况下提高生产效率与稳定性。
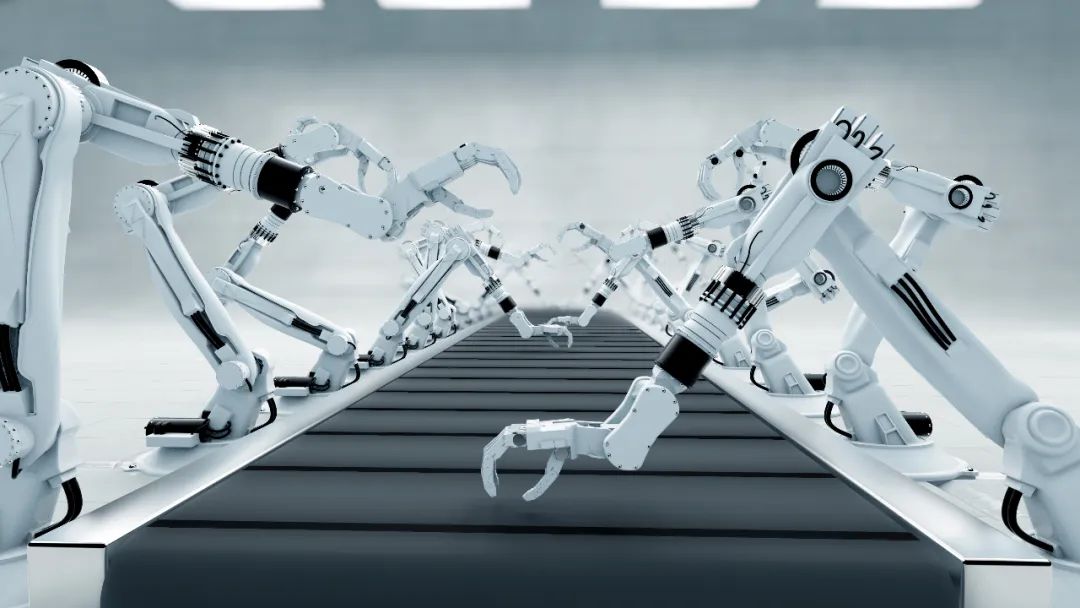
第五,对现有的各工艺信息系统进行集成,实现单一数据源,保证互联互通。实现所有业务在统一平台下的运作是工业4.0的重要目标之一,此前我们在信息化建设方面投入了很多资源,尤其是工艺信息化,在各项业务中,工艺信息化的水平是比较高的,但现有的信息化建设缺乏整体的统筹策划,各信息系统相对独立,没有共享信息资源,形成了一个个信息孤岛,对于提升整体业务效率造成了很大障碍。因此,现在需要我们站在公司整体的层面,对工艺信息系统进行统一平台的集成工作,将信息化系统的作用真正发挥出来。在实现工业4.0的道路上,我们要走的路还很长,要补的课还很多,但这些都不是问题,只要我们抓住机遇,制定切实可行的计划,一步一个脚印地前进,在这一过程中我们就可以提高自己,这样工业4.0也会离我们越来越近。
文章来源:APS研究会
免责声明:本文系网络转载,版权归原作者所有。但因转载众多,无法确认真正原始作者,故仅标明转载来源。本文所用视频、图片、文字如涉及作品版权问题,请第一时间告知,我们将根据您提供的证明材料确认版权并按国家标准支付稿酬或立即删除内容!本文内容为原作者观点,并不代表本公众号赞同其观点和对其真实性负责。